自動化・FAの導入事例
組立自動化・FA導入事例:ゴム栓挿入装置
従業員規模約700名の自動車部品工場における生産ラインの効率化を目的として導入いただきました。
多品種少量生産を行っており、頻繁なライン変更やセットアップが課題となっていました。
【導入の経緯】
複数種のコネクタ用パーツフィーダを複数台用意すると、多くのスペースを占め、かつ費用が増えかねないと考えていました。省スペースで自動化実現したいとのご要望を受け、ロボット+カメラによるコネクタを取り出しの多品種対応をご提案。パーツフィーダ複数台に比べ、設置面積を大幅に削減することができました。
【導入後の効果】
・ゴム栓挿入装置導入で2名の省人化を実現
・サイクルタイムは手作業と比較し200%アップ
・2.6年で設備の投資額を人件費の削減額が上回る
【導入設備の概要】
ワークへ防水ゴム栓を挿入する装置です。
① ゴム栓を2種のパーツフィーダーで整列させ、挿入ステーションへ圧送。
② モートロンのピッキングフィーダーでワークをピッキングしやすいよう分離させ、 カメラ付きのロボットでピッキングします。
③ 前工程でピッキングしたワークを挿入ステーションへ搬送、圧送されたゴムをエアシリンダで挿入します。
④ ゴム栓を挿入したワークを検査ステーションへ搬送。カメラにて画像検査を実施。
⑤ 排出。
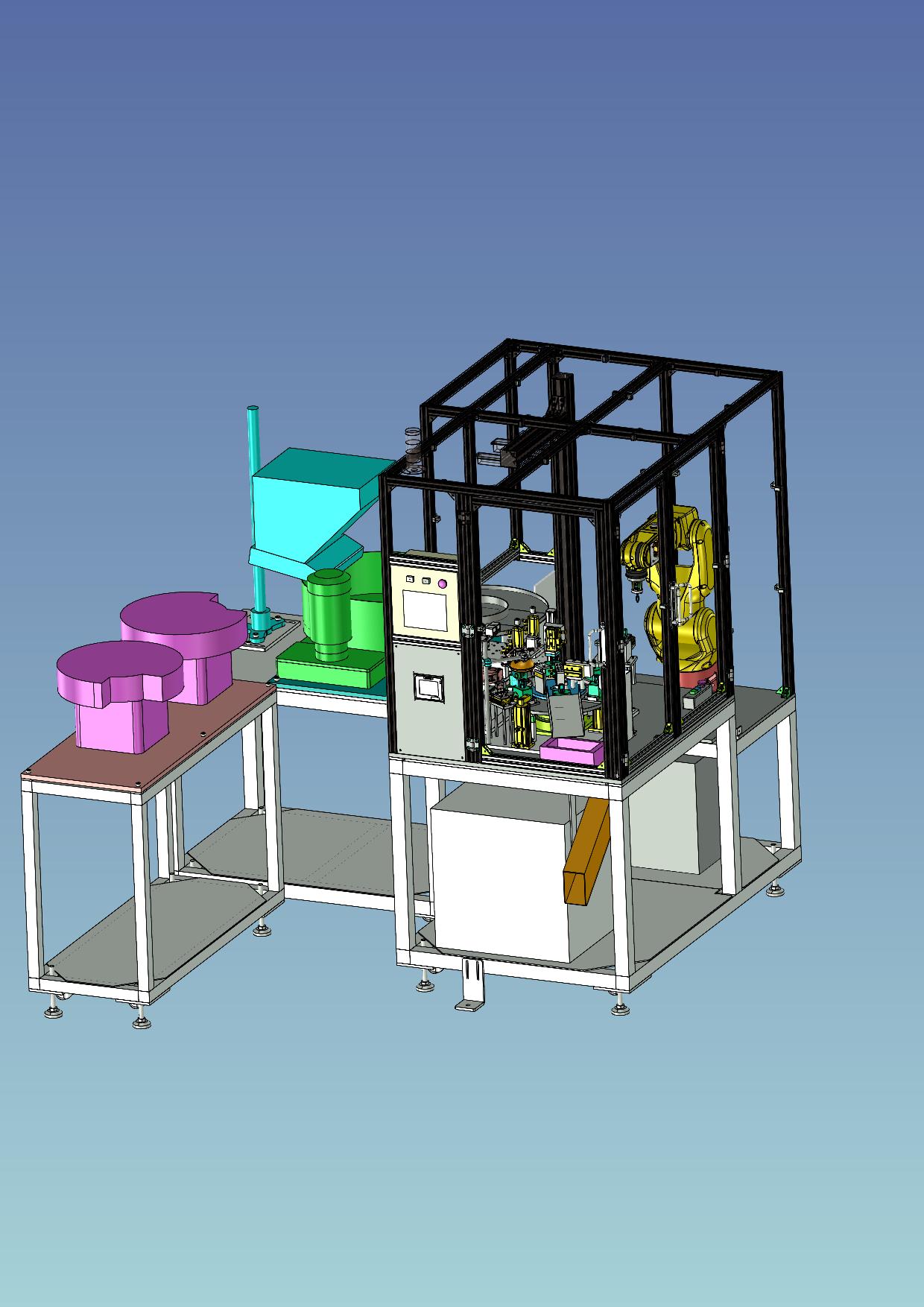
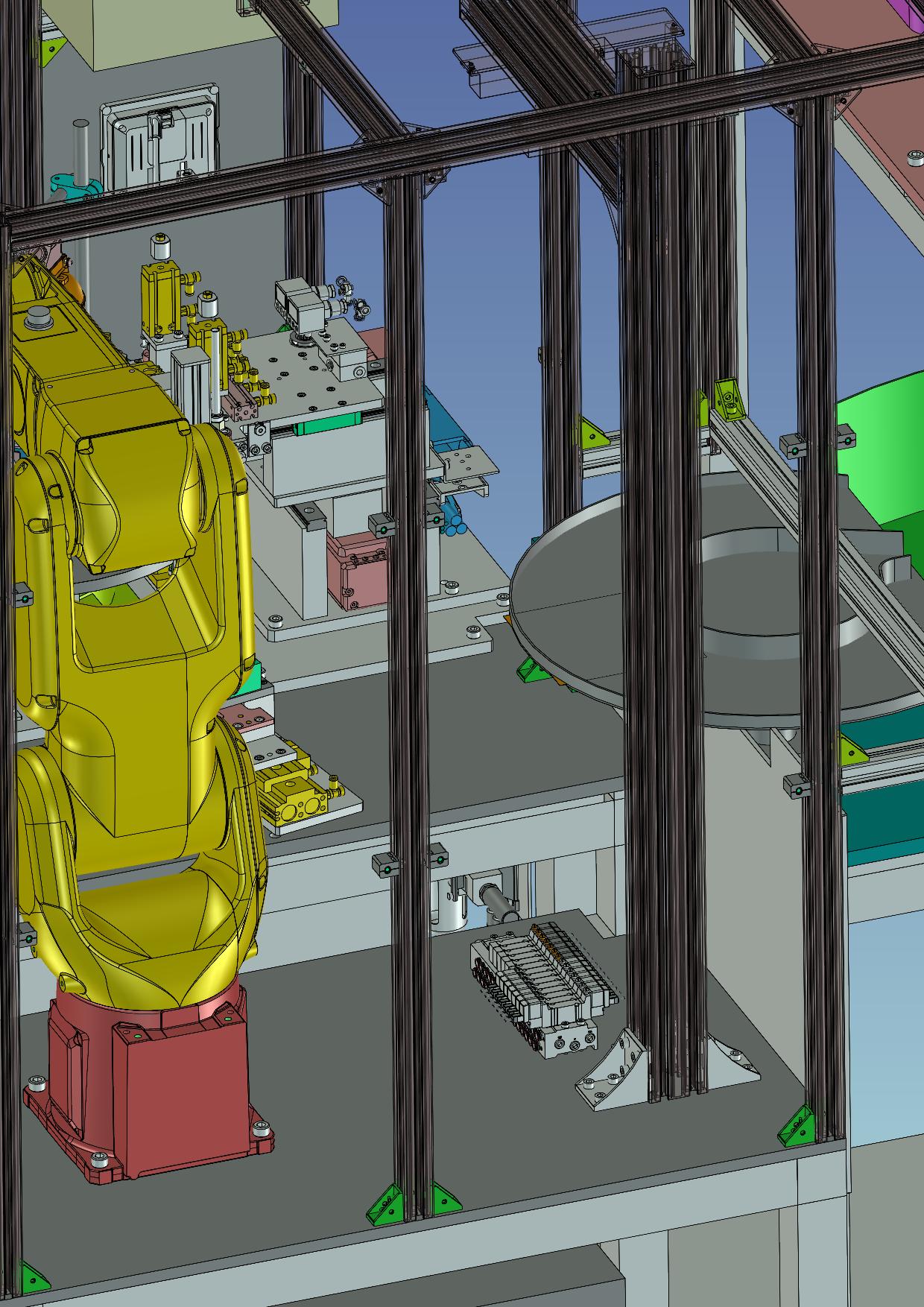
詳しくはこちらから→採用事例:ゴム栓挿入装置 導入による省人化